GE Aviation gets FAA Certification for First 3D Printed Jet Engine Part
- BY Lav Radis
- May 4, 2015
- 2 min read
Source: www.3dprinting.com
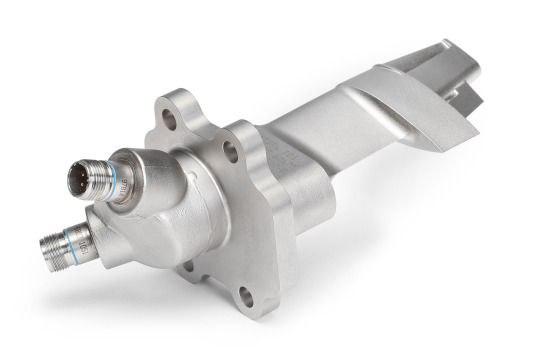
3D printed T25 sensor enclosure unit produced by GE Aviation and certified by FAA. Image credit: GE Aviation
A few weeks ago General Electric announced that the FAA (U.S. Federal Aviation Administration) cleared their first 3D printed part to fly.
The fist-sized T25 housing for a compressor inlet temperature sensor was fabricated by GE Aviation and will be retrofitted to over 400 GE90-94B jet engines on Boeing 777 aircraft.
The laser sintered housing protects the compressor inlet temperature sensor’s fine electronics from icing and damaging air pressure inside the jet engine. Certification means that this part is now suitable to be mounted into commercial jet engines from GE.
GE is currently partnering with Boeing to install this new part in over 400 of its GE90-94B engines used on the new high-tech Boeing 777 aircraft.
Naturally GE Aviation is not stopping on a single part. Here is a video from GE Aviation on their next part to be installed into LEAP jet engines, the 3d printed fuel nozzle. This 3d printed part is five times as durable as regularly produced one, 25% lighter, runs cooler because of internal cooling structures, only one part instead of 18.
GE report writes:
"It would normally take GE several years to design and prototype this part, but the GE team was able to shave as much as a year from the process. “The 3D printer allowed us to rapidly prototype the part, find the best design and move it quickly to production,” says Bill Millhaem, general manager for the GE90 and GE9X engine programs at GE Aviation. “We got the final design last October, started production, got it FAA certified in February, and will enter service next week. We could never do this using the traditional casting process, which is how the housing is typically made.” Jonathan Clarke, program manager for the project, says that the team ended up with a faster and simpler design, and superior material properties. “Once we found a workable solution, it went straight to production,” Clarke says. “This technology is a breakthrough.”
GE Aviation is also heavily investing in additive manufacturing with their factory in Alabama:
Aerospace industry is becoming the main driver of additive manufacturing adoption and real-life application in critical infrastructure. If you find this story interesting check out other post about Boeing patents or China Eastern Airlines 3D printed parts.
Image Source: GE Aviation
Comments